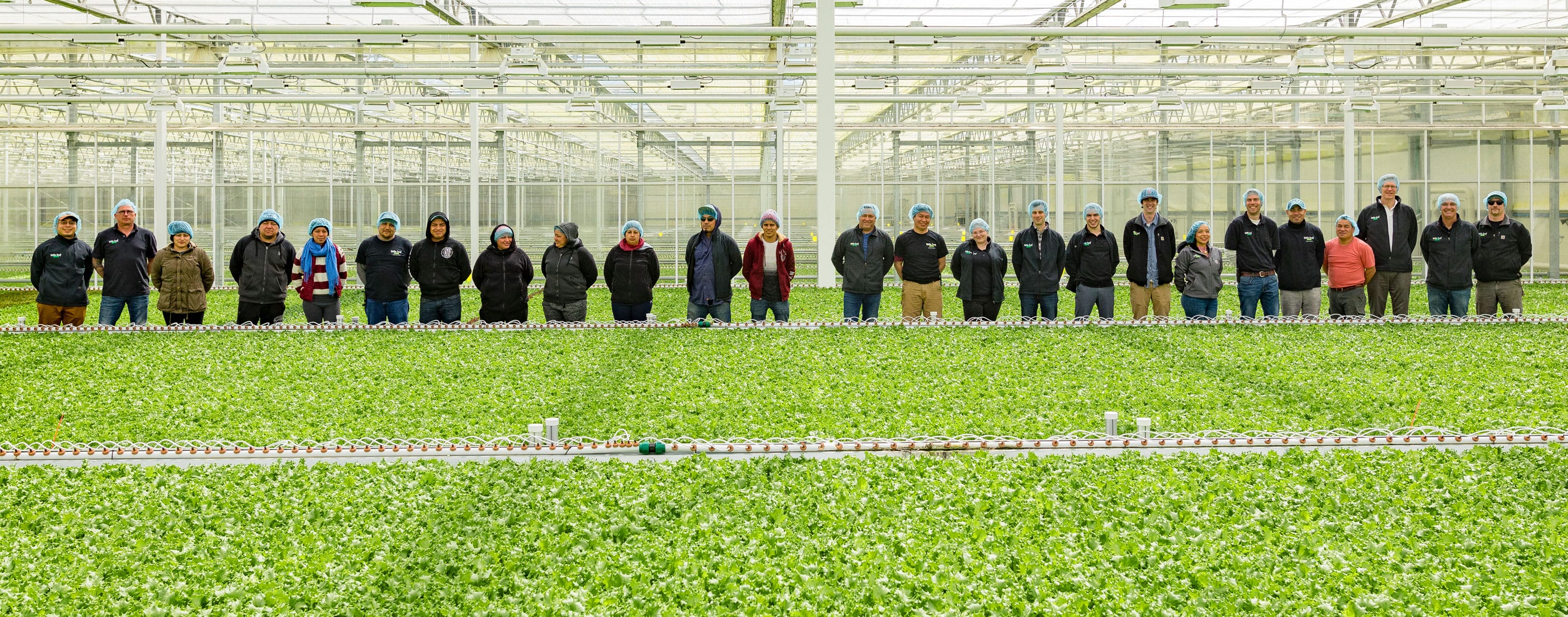
Grantee Profile
Lettuce Keep Greens Local
Using a sustainable, hydroponic system to produce year-round, fresh, and local lettuce alternatives for New England consumers.
In the world of leafy greens, California and Arizona are the biggest growers on the block – together producing 90 percent of the country’s lettuce. For New England consumers, those boxes and bags of greens can take upwards of ten days to get from the field to the supermarket shelf. Not only that, but more than three gallons of water are required to grow a single head of lettuce through traditional, in-the-ground farming methods. Paul Sellew noticed the lack of year-round, fresh, tasty, and local lettuce alternatives for New England consumers and decided it was time for a new grower to step in.
Already an experienced entrepreneur in the New England agriculture and organics recycling spaces, Sellew co-founded Little Leaf Farms in Devens, Massachusetts in 2016 with now-Executive Vice President of Sales and Marketing Tim Cunniff. Cunniff has been in the produce sales business for 29 years. (“I’m a produce guy. It’s what I do.”) From pineapple, to bananas, to tomatoes, he’s sold it all. Sellew and Cunniff had worked together before at Sellew’s previous venture, Backyard Farms greenhouse tomatoes. Now, the duo has shifted its focus to baby lettuce (adolescent lettuce, if you want to get technical), which Little Leaf Farms grows hydroponically inside its state-of-the-art greenhouse.
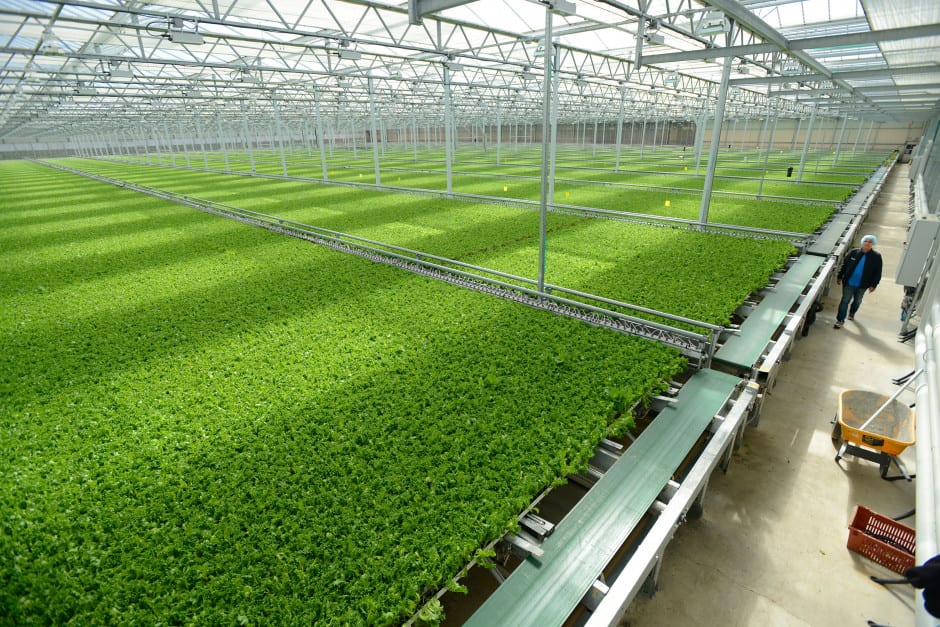
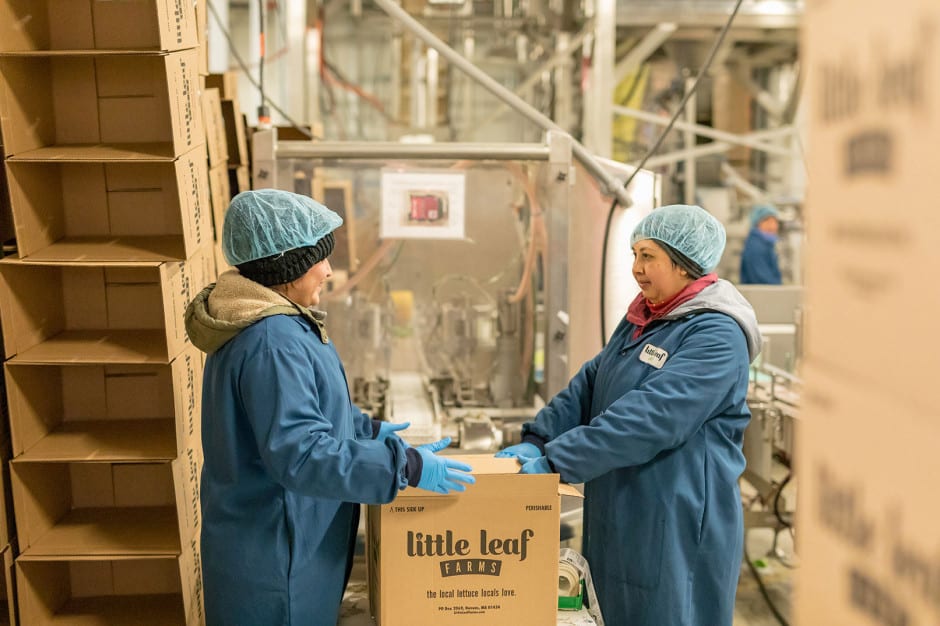
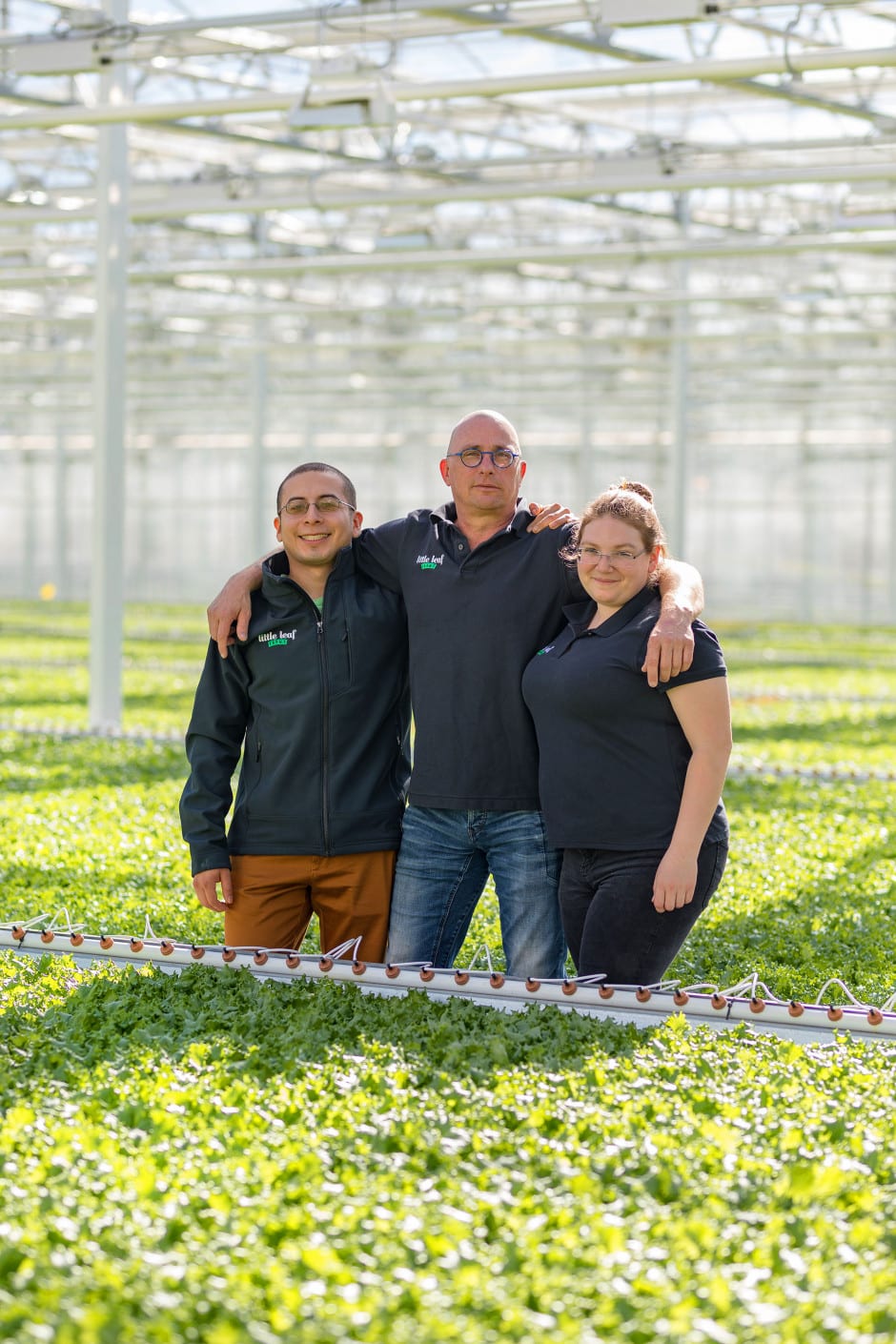
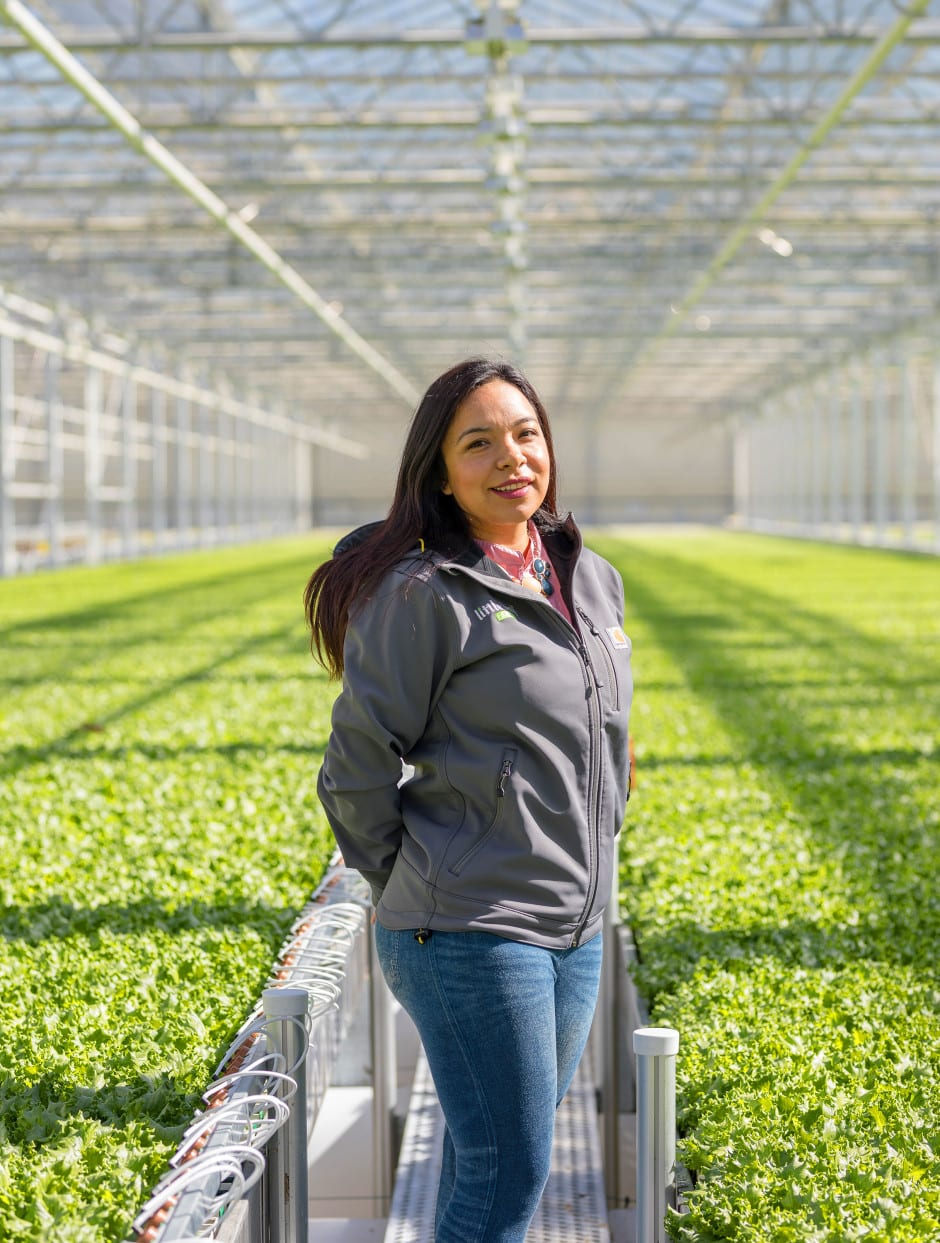
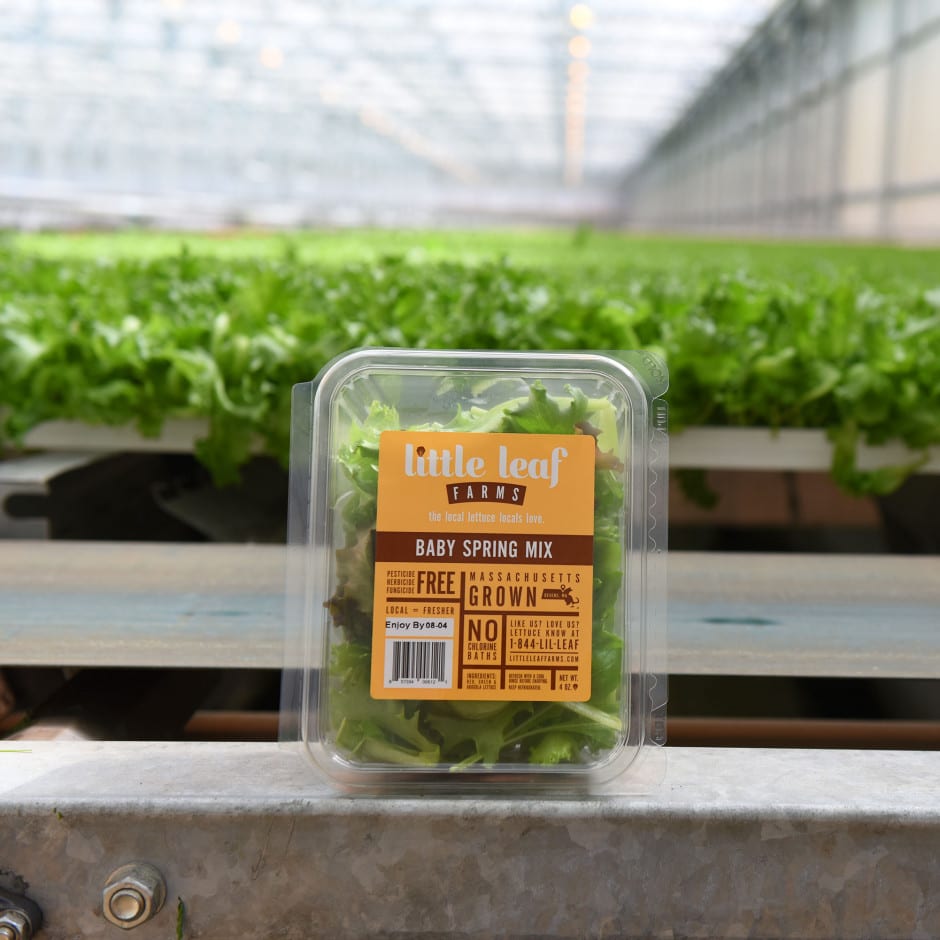
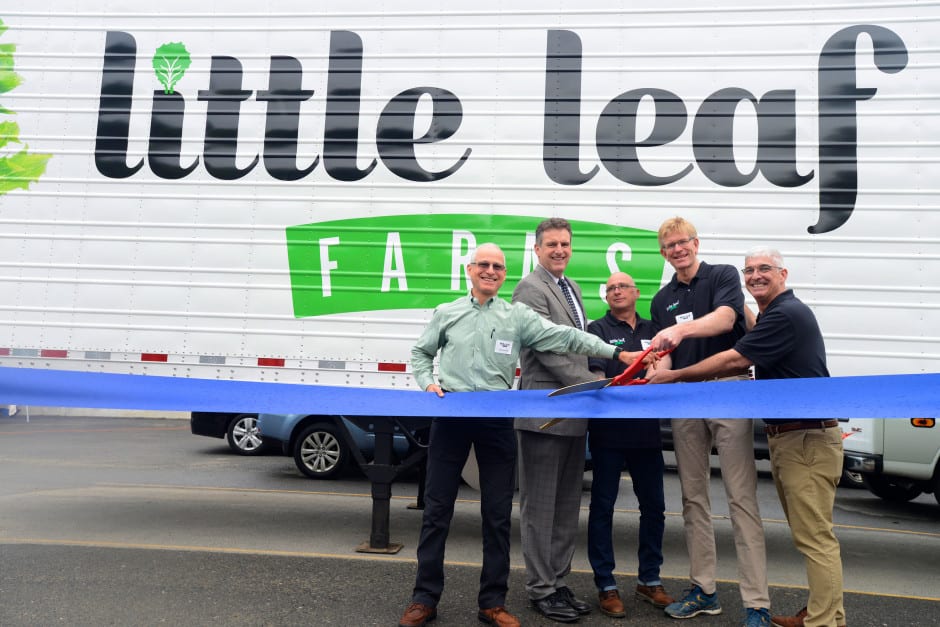
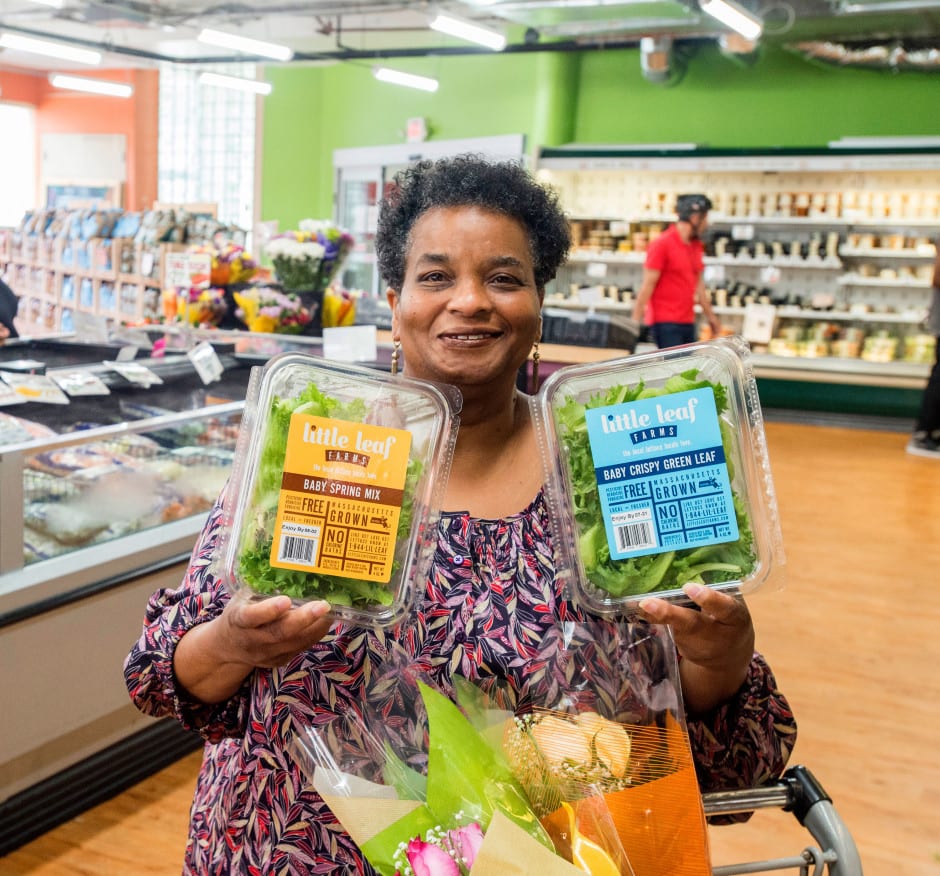
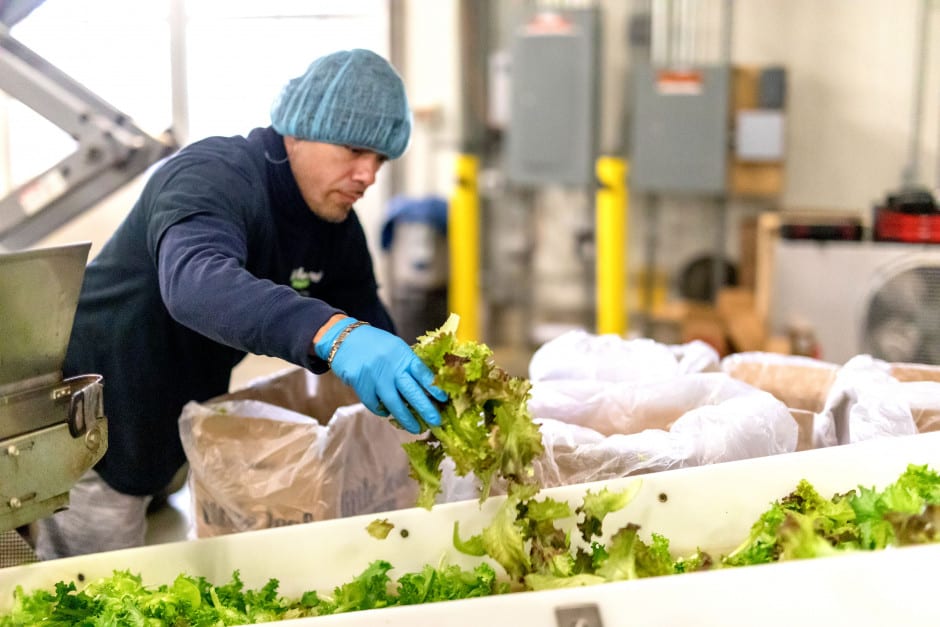
“Hydroponic” growing is defined as crop cultivation without the use of soil. Instead, growers nourish plants with nutrient- and mineral-enriched water. The technology and processes behind Little Leaf Farms’ hydroponic system draw inspiration from other producers in Finland, the United States, the Netherlands, and Belgium. Not satisfied with simply duplicating existing methods, however, Sellew and Little Leaf Farms’ Head Grower and Manager, Pieter Slaman, are focused on innovation: they’re using a closed hydroponic greenhouse model, whereby inputs like water are continuously recycled through the greenhouses – as well as prioritizing sustainable energy and water use.
Slaman hails from the Netherlands’ Westland region and has been in and out of the greenhouse business since age 17. Like many Westland youth, Slaman grew up thinking about balancing inputs and outputs in greenhouse horticulture, which is why he believes so strongly in organic agriculture and the work that Little Leaf Farms is pioneering. As Sellew was beginning to envision what Little Leaf Farms would look like, he brought Slaman on board to help develop the more technical side of the operation.
The Netherlands’ greenhouse industry is years ahead of that of the United States. With the northern country’s cold climate, short growing season, and mostly urban population, its economy has come to depend on greenhouses for fruit and vegetable production. More than half of the Netherlands’ terrain – which occupies about the same land area as Massachusetts – is used for agriculture and horticulture, with 54,840 farms in 2017. The Netherlands is also the second largest food exporter in the world, such that 80 percent of its greenhouse horticulture depends on exports, primarily to the European Union. Greenhouse growing is mostly hydroponic, explains Slaman, primarily because of the agricultural sector’s movement away from pesticide and insecticide chemical use over the past few decades.
The greenhouses at Little Leaf Farms perform a balance of natural cycles and intelligent automation to produce their hydroponic lettuce. Inside the facility, smells of wet concrete and knotted roots and the rhythmic churning of automated levers and conveyor belts mingle in the heavy, warm air. Against a backdrop of grey and white, vibrantly lush green lettuce stretches across five acres split between two greenhouses. The leaves are embedded in strips of a dense, inorganic, mineral wool called rockwool. Listening closely, one can hear the 55,200 (that’s 2,400 rows of lettuce across 23 sections) streams of nutrient-rich water trickling into each tilted lettuce gutter at regular intervals. Slaman creates his own fertilized water samples every week, mixing nitrogen, phosphorus, and potassium to ensure that the lettuce gets everything its needs and nothing that it doesn’t.
Expert hands control the heating, cooling, CO2 enhancement, humidity, and light of this almost entirely closed system. Only 27 inches of rainwater run and re-cycle through the greenhouses each year. The goal, says Sellew, echoing what he has learned from Slaman, is to “create an environment that takes away all the stressors for the plants,” so that they can just do what they know how to do: grow. To walk down a line of soil-less gutters is to walk through the life-cycle of a lettuce plant, but in reverse; heads of lettuce age backwards into pinkie-sized sprouts, perched atop their rockwool growing material. Sensors and levers push each gutter of lettuce forward every few minutes, culminating in the adolescent lettuce that the farm harvests, packages, distributes, and sells. The whole process takes under thirty days, varying with the season and the greenhouse in which a given lettuce crop is grown.
Sellew emphasizes that Little Leaf Farms is pioneering systems of intelligent automation, not just mechanization. What makes this automation “intelligent”? Intelligent automation at Little Leaf Farms means “line balance”: whenever a gutter of lettuce leaves its row for harvesting, another gutter with sprouting seeds fills in at the back of the line. Then, when the plants reach a certain size, gutters begin to leave small gaps between one another so that the growing leaves don’t shade their neighbors. Human hands never touch the lettuce, which guarantees food safety and disease prevention. Meanwhile, sensors count individual photons of sunlight every day to ensure that from summer to winter, the plants receive the same amount of light (natural or artificial) every day. Finally, as water drains from each lettuce gutter, it runs through a sanitation system of filter paper, oxygenation, and UV disinfection before being re-enriched with nutrients (per Slaman’s weekly formulation) and recycled back into the hydroponic irrigation system.
“You have to run a greenhouse on time,” Slaman emphasizes. “If [it’s] not on time, you have no greenhouse.” In addition to all the machinery running on schedule, that means labor, materials, and lettuce harvesting must all also be punctual and responsive, seven days a week. Slaman thinks it is vital to cultivate buy-in from the farm’s staff on the importance of timing. Everyone has to agree that better timing translates into better quality if the whole team is to feel genuinely invested in Little Leaf Farms’ mission. The technology operators and growers also must be motivated not just to rely on the data they receive from their computers; they can only effectively respond to those messages about the greenhouses if they are tuned into the plants themselves. “It’s mostly feeling,” says Slaman of greenhouse farming. “A plant will tell you if it’s having fun or not,” and lettuce is one of those plants that will tell you very quickly. “The plant is really in control…[they] know how to grow.”
Little Leaf Farms knows how to grow its business too. The company is rapidly expanding its share of the New England market, sprinting to keep up with consumer demand. While Slaman works his magic as the grower behind the curtain, Cunniff is out getting Little Leaf lettuce onto grocery store shelves. But the produce market is a crowded space. It took Little Leaf Farms over six months to break in. Cunniff explains that packaged lettuce acts like a consumer packaged good in the grocery store – it is an item used daily by customers and thus needs to be replaced regularly on the shelf. Stores fill in what they sell, so Little Leaf Farms had to become what consumers consistently picked. Printed in-store signage documenting food miles, a redesigned label that addresses consumers’ most pressing questions (including where the lettuce is grown and with what chemicals it is treated – none), a consistently high-quality product, and availability at over 1,000 grocery stores have made it easy for its broadening consumer base to select and stick with Little Leaf Lettuce over the past two years.
Word of mouth also helps, and Cunniff says that Little Leaf Farms has accumulated “a cult-like following” of avid lettuce lovers. These enthusiasts flood Little Leaf Farms’ Facebook, email, and phone number daily with praise and gratitude for the company and their promises to spread the word about Little Leaf’s lettuce. Momentum over the last two years has allowed demand for Little Leaf lettuce to outpace supply, prompting the farm’s recent expansion into a second, redesigned greenhouse. The new facility doubles the farm’s growing acreage and allows staff to implement small changes based on learnings from the first greenhouse. Phase three of expansion is already in the works for 2019, which will again double production. Diversification of product will come eventually – consumers are demanding it – but Slaman and Sellew say they want to ensure sustainable quality and consistency at their new scale before testing new products. “Consumers rule” at Little Leaf Farms, according to Sellew, and growing local isn’t enough – the superior quality, competitive price, and sustainable company values have to be there too.
Little Leaf Farms is both setting an example of what a regional, sustainable food system can look like, and building out a pipeline of fresh talent to ensure its long-term viability. A steady stream of young growers runs through Little Leaf Farms from the Cornell College of Agriculture and Life Sciences’ Controlled Environment Agriculture Program. “You have to grow your own growers,” explains Cunniff. At Little Leaf Farms, these young professionals learn to think of the nebulous concept of “sustainability” across three facets: a low carbon footprint, biological plant and disease management practices, and high-quality relationships between people. “The systems that survive will be sustainable,” asserts Sellew, and Little Leaf Farms is positioned to provide that sustainable food production model for the entire region. Thus, as Slaman trains his fresh talent, he hopes that they will not only help Little Leaf Farms thrive, but also eventually go on to operate their own greenhouses. “It’s just scale, scale, scale,” says Cunniff.
It is an unusual case at Little Leaf Farms, where scaling up means more sustainability rather than less. And the farm is on course to continue its rapid expansion through the end of the decade. What remains to be seen, however, is exactly what kind of influence the Little Leaf Farms model will have over New England’s changing agricultural sector. Just as the team nurtures their lettuce, their ambition is to help produce a regional agricultural framework that allows sustainable growers to thrive at-scale. With luck (and a lot of hard work), their ongoing disruption of traditional agriculture and produce markets will establish conditions for innovative New England farms to just do what they know how to do: grow.
Click Here to watch a video detailing the story of Little Leaf Farms!
It’s mostly feeling. A plant will tell you if it’s having fun or not, and lettuce is one of those plants that will tell you very quickly. The plant is really in control…[they] know how to grow.